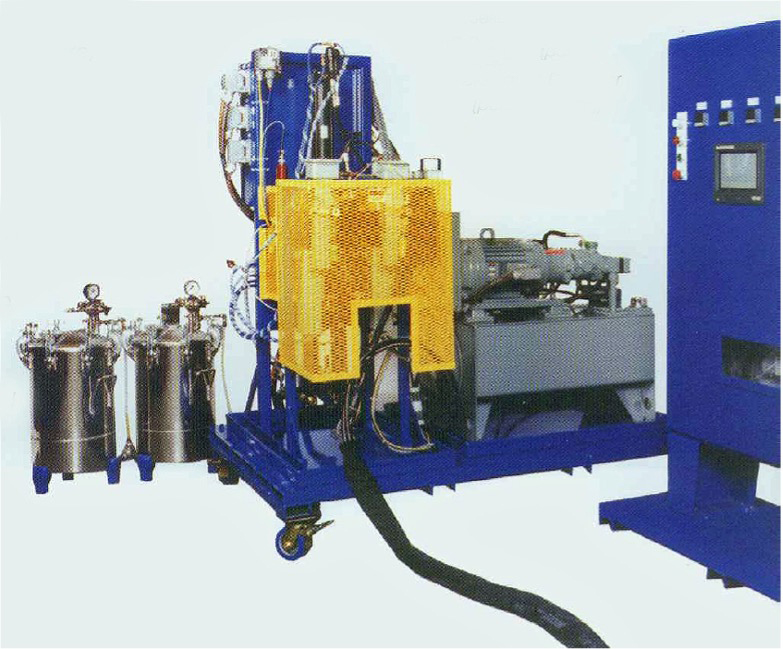
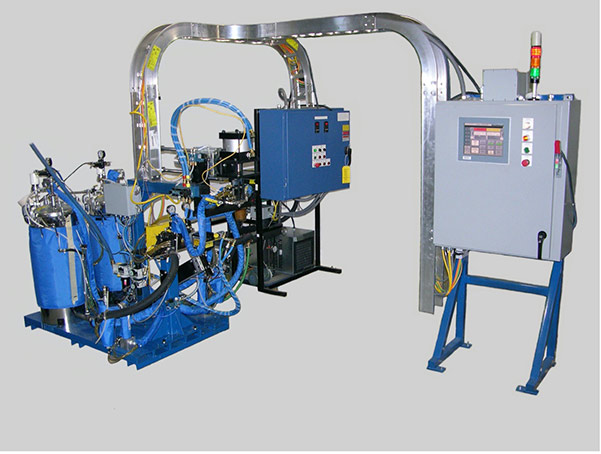
Positive displacement, single acting, fixed ratio lance piston meters ensure on ratio proportioning and accurate shot delivery. Meter capacities are sized for production requirements.
Power flow valves for both the inlet and outlet of each meter ensure that fluids are displaced to the gun accurately and on ratio.
Metering Unit is hydraulically powered with electronically adjustable constant flow rate technology. This provides a powerful and robust drive package that maintains material flow rates even against variable loads. Time required to dispense a shot is always repeatable.
Closed loop feedback control of metering unit provides a very high degree of shot size consistency.
Flush sensing, high accuracy pressure transducers are used to monitor and control material pressures at all times to ensure a stable process.
Common dual circuit Hydraulic Power Unit provides all the power for both the Metering Unit and Impingement Mix Gun. This helps conserve floor space and reduces equipment costs.
Impingement Mix Gun is hydraulically powered to minimize weight and size as well as to maximize operating power and reliability of gun.
Impingement Mix Gun includes:
- Hardened and precision lapped Tool Steel mix head components for reliably good mix and long service life with minimum maintenance.
- Choice of pistol grip or parallel handle trigger designs for optimized ergonomic manual applications.
- Heated gun maintains temperature during idle periods, thus requires no test shots when production resumes.
- Gun Open and Closed position sensors for proper sequencing with dispenser controls.
- Quick disconnects on all cables for ease of service.
Entire system is heated as required from supply source to dispense tip and controlled using PID temperature controllers for each heated zone. Primary heated zone utilizes fluid heaters and probe type sensors inserted into the fluid stream for high heating capacity and precise temperature control.
Each heated zone includes a redundant over-temperature controller complete with its own separate temperature sensor for safety backup.
Heated Hose Bundle connects the dispenser to the gun and is available in lengths to suit the application. Designed to minimize size and weight of the assembly in order to maximize flexibility and ergonomics, yet is built with components rated for continuous flexing in order to maximize reliability and minimize maintenance required.
One Heated Hose Bundle and Gun per system is standard. A Dual Gun (DG) option is available for manual dispensing applications. This option provides online hot backup capability.
Nema 12 rated PLC Control Panel built to “generic automotive” (JIC) standards controls all dispenser functions. Allen-Bradley PLC is standard. Other PLC’s and custom panel designs available upon request.
Door mounted Color Touchscreen is provided for HMI / MMI functionality. The Touchscreen is also utilized for password protected access to adjustable parameters such as Shot Setups, Sequence Setups, etc. An optional Remote Operator Station (ROS) is available. Other brands and types of touchscreens available upon request.
16 programmable shot sizes are available as standard. Additional programmable shot sizes available upon request.
4 programmable 12 step sequences are available as standard. More and / or longer programmable sequences are available upon request.
The N-3300 series Foam Dispensers are available with many other optional features and hardware packages that facilitates their integration into a foam dispensing cell, such as:
- Tool Tip Cleaners for cleaning the gun dispense tip.
- Hose Management Systems for suspending and retrieving the Heated Hose Bundles improves the ergonomics of a manual application as well as extends the life of the bundle through proper routing and retrieving of hoses in a manual or automated application. Also provides a safety feature to stop the conveyor if the hose is entangled with a moving body.
- Material Supply Packages such as; totes, pumps, pressure pots, etc., for supplying the materials to the dispensers.
- Networking / interfacing the dispensers to other controllers such as; robots, cell controllers, automatic vehicle identification systems, process verification systems, factory information systems, etc., through many types of interfaces and networks such as; discrete I/O, Remote I/O, Data Highway Plus, DeviceNet, ControlNet, Ethernet, etc.